Porosity in Welding: Identifying Common Issues and Implementing Finest Practices for Avoidance
Porosity in welding is a prevalent issue that frequently goes unnoticed up until it triggers considerable issues with the honesty of welds. In this conversation, we will check out the crucial aspects adding to porosity development, examine its damaging impacts on weld performance, and talk about the finest methods that can be adopted to reduce porosity occurrence in welding processes.
Usual Root Causes Of Porosity

Using dirty or damp filler products can introduce impurities into the weld, adding to porosity problems. To reduce these common causes of porosity, extensive cleaning of base metals, appropriate shielding gas choice, and adherence to ideal welding parameters are important techniques in accomplishing premium, porosity-free welds.
Impact of Porosity on Weld High Quality

The existence of porosity in welding can significantly endanger the structural honesty and mechanical properties of bonded joints. Porosity develops spaces within the weld steel, compromising its total strength and load-bearing ability. These spaces act as tension focus points, making the weld extra susceptible to splitting and failure under applied lots. Additionally, porosity can minimize the weld's resistance to deterioration and other environmental variables, even more reducing its long life and performance.
One of the primary repercussions of porosity is a reduction in the weld's ductility and strength. Welds with high porosity levels have a tendency to show reduced impact toughness and lowered ability to deform plastically before fracturing. This can be particularly concerning in applications where the welded parts go through dynamic or cyclic loading conditions. Porosity can impede the weld's ability to effectively transmit pressures, leading to early weld failing and prospective security risks in vital structures. What is Porosity.
Finest Practices for Porosity Prevention
To improve the structural integrity and quality of bonded joints, what details procedures can be applied to lessen the incident of porosity during the welding additional hints process? Porosity avoidance in welding is vital to make sure the stability and strength of the last weld. One efficient method is proper cleansing of the base steel, removing any impurities such as rust, oil, paint, or moisture that can cause gas entrapment. Guaranteeing that the welding equipment remains in great problem, with tidy consumables and appropriate gas circulation rates, can additionally substantially decrease porosity. Additionally, preserving a stable arc and regulating the welding specifications, such as voltage, existing, and travel rate, helps develop look at this website a constant weld swimming pool that reduces the threat of gas entrapment. Utilizing the proper welding method for the details material being bonded, such as adjusting the welding angle and weapon position, can better avoid porosity. Normal examination of welds and immediate removal of any type of concerns recognized throughout the welding procedure are essential methods to protect against porosity and generate top quality welds.
Significance of Appropriate Welding Methods
Carrying out appropriate welding methods is vital in making sure the architectural stability and high quality of welded joints, developing upon the foundation of effective porosity avoidance actions. Welding strategies straight affect the general strength and resilience of the welded framework. One vital facet of appropriate welding techniques is maintaining the proper warmth input. Extreme warm can lead to increased porosity as a result of the entrapment of gases in the weld swimming pool. On the other hand, insufficient warmth might result in insufficient combination, creating possible powerlessness in the joint. Additionally, making use of the proper welding specifications, such as voltage, current, and take a trip speed, is important for achieving audio welds with very little porosity.
Additionally, the selection of welding process, whether it be MIG, TIG, or stick welding, ought to straighten with the specific demands of the task to ensure ideal outcomes. Proper cleaning and prep work of the base steel, as well as selecting the ideal filler product, are also vital parts of proficient welding techniques. By adhering to these finest techniques, welders can decrease the risk of porosity formation and produce top notch, structurally audio welds.
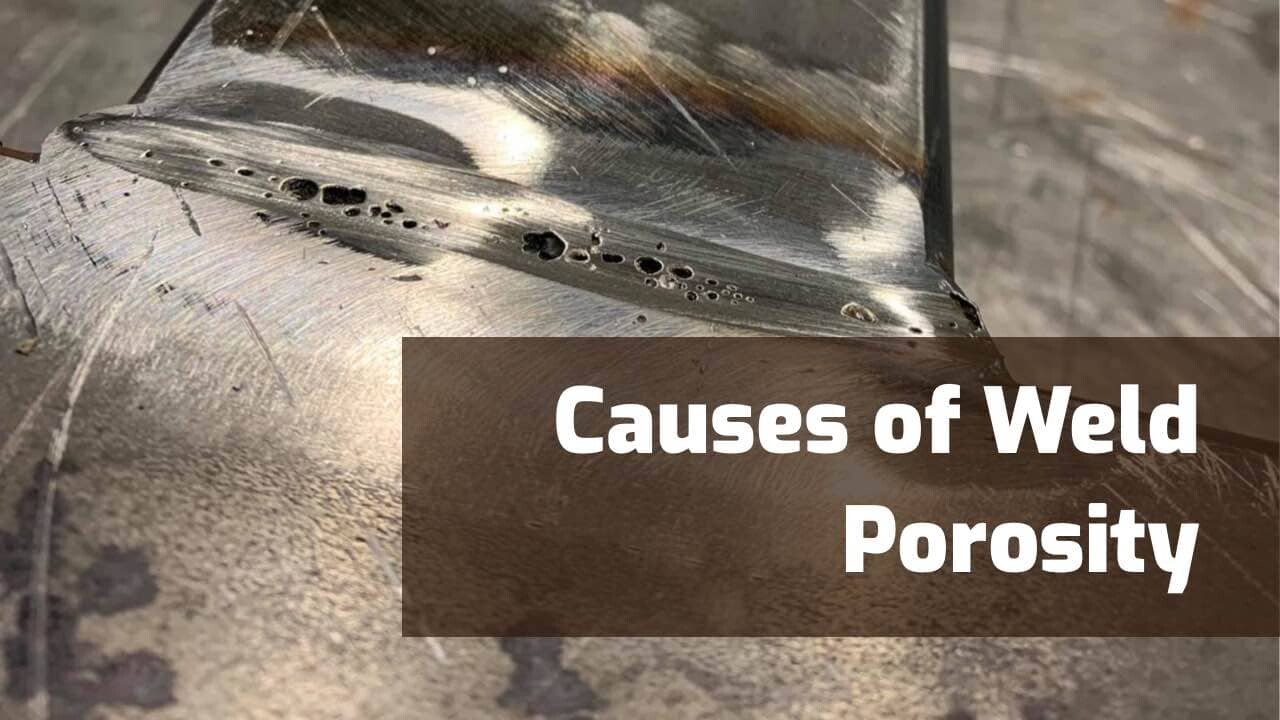
Examining and Quality Assurance Measures
Examining procedures are crucial to find and protect against porosity in welding, ensuring the stamina and sturdiness of the final item. Non-destructive testing methods such as ultrasonic screening, radiographic testing, and aesthetic evaluation are commonly utilized to identify possible problems like porosity.
Post-weld assessments, on the other hand, examine the final weld for any type of problems, including porosity, and confirm that it meets specified criteria. Applying a thorough top quality control strategy that consists of extensive testing procedures and inspections is paramount to lowering porosity concerns and making sure the general quality of bonded joints.
Verdict
In final thought, porosity in welding can be a typical issue that influences the high quality of welds. By identifying the common root causes of porosity and carrying out best techniques for avoidance, such as proper welding strategies and testing measures, welders can make certain high top quality and reputable welds. It is necessary to focus on Read Full Report prevention approaches to lessen the occurrence of porosity and keep the integrity of bonded structures.